Wooden boat varnish: the best protection and finish
Choosing the right varnish for a wooden boat is an essential step. It guarantees not only the boat’s aesthetic appeal, but also its durability in marine conditions. External aggressions such as salt water, ultraviolet (UV) rays and climatic variations progressively weaken wood, making it more vulnerable to cracks and moisture infiltration. That’s why a good varnish must offer effective protection against these elements, while preserving the wood’s natural appearance.
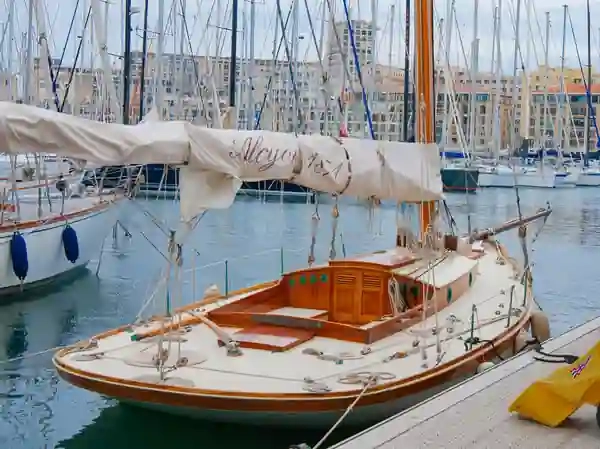
Conventional single-component varnish
Among the various types of existing varnish, traditional single-component varnish is one of the most widely used. Often based on alkyd or urethane resin, it is valued for its ease of application and glossy finish, which enhances the texture of the wood. This type of varnish builds a flexible protective layer that follows the natural movements of the wood. This makes it ideal for areas prone to variations in temperature and humidity.
However, to guarantee optimum protection, ten coats are required, and regular maintenance is essential. This varnish can flake over time, requiring frequent retouching to avoid alteration of the underlying wood.
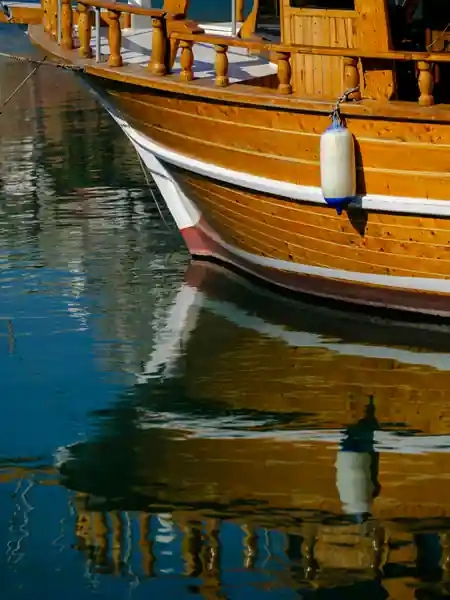
Two-component polyurethane varnish
Two-component polyurethane varnish is an alternative offering more resistant protection. Composed of a resin and a hardener, it creates an extremely hard, durable finish, perfectly suited to extreme marine conditions. Its resistance to UV rays, chemicals and abrasion makes it the preferred choice for boats exposed to strong sunlight and salt water.
However, it’s more complex to apply. It requires precise dosing of the mixture to avoid the appearance of bubbles or poor bonding. Because of its rigidity, this type of varnish is less suitable for wood that undergoes a lot of mechanical stress, as it risks cracking over time.
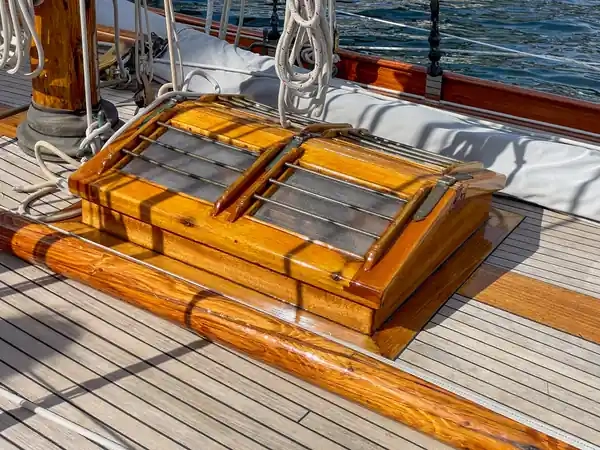
Epoxy varnish
Another particularly popular type of varnish is epoxy varnish. It’s actually an epoxy resin used mainly as a primer to waterproof wood. This type of varnish creates an extremely effective barrier against humidity and water infiltration. It is therefore particularly suitable for areas of the boat that are frequently submerged or exposed to severe marine conditions.
Epoxy does have one drawback, however: on its own, it is not resistant to ultraviolet radiation. You’ll need to protect it with a finishing varnish, such as a polyurethane or traditional varnish, to prevent yellowing and degradation due to sunlight. This is especially crucial if sailing in tropical waters.
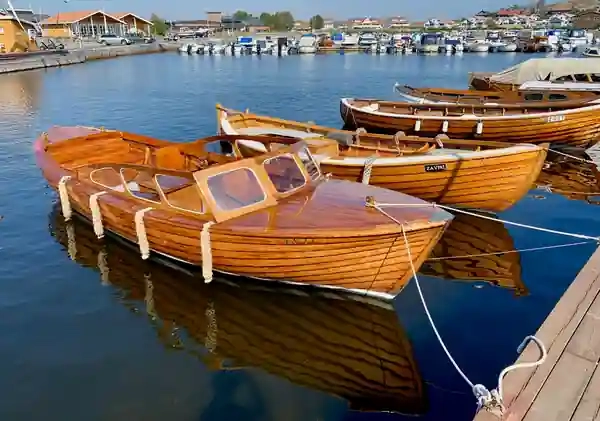
Saturators and oils
Oil-based saturation products represent a more natural alternative to traditional film-forming varnishes. Unlike the latter, which create a protective film on the surface, saturation penetrates deep into the wood’s fibers to nourish it and provide lasting protection against humidity. This treatment enables the wood to remain elastic and retain its natural, untreated appearance, while limiting the risk of cracking. Saturation is particularly well-suited to exotic woods such as teak, often used in shipbuilding. Tung oil or linseed oil enable them to benefit from an in-depth treatment that respects their natural properties.
However, while saturators offer good water resistance, they are more sensitive to UV rays and require regular maintenance. Repeated applications are essential to maintain their effectiveness and protection over time.

Types of finish
When it comes to aesthetics, there are several types of finish to choose from, depending on the desired effect. Gloss varnishes are the most commonly used, as they enhance the depth and natural nuances of the wood while offering excellent protection against external aggression. However, they can emphasize imperfections in the substrate and require thorough maintenance to maintain their brilliance.
Satin or matt varnishes, on the other hand, offer a more discreet, natural finish. They are ideal for those who want a more authentic look, while benefiting from effective protection against humidity and UV rays. These finishes are available in classic, polyurethane or epoxy versions, depending on the level of protection required.
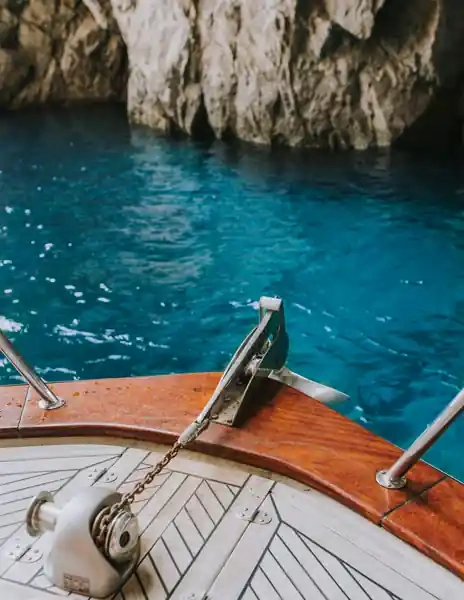
Varnish preparation and application
Varnish application is a crucial step which determines the quality and durability of the final result. Before varnishing a wooden boat, careful preparation of the substrate is essential. The wood must be carefully sanded to obtain a perfectly smooth surface, free of asperities. A thorough dusting is then necessary, followed by degreasing with a suitable solvent. Acetone or alcohol can be used to remove all traces of residue that could compromise varnish adherence.
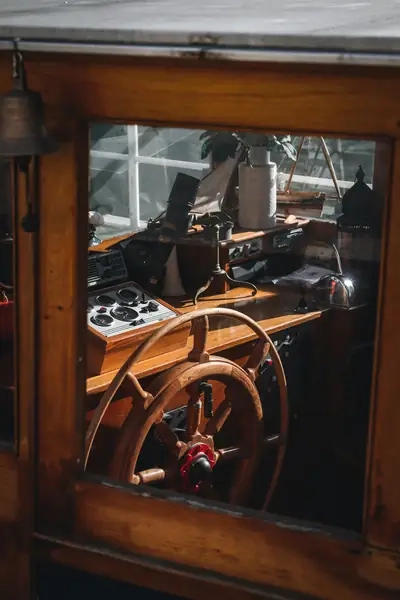
Dilute the first coat of varnish with thinner to penetrate the wood fibers and create optimum adhesion for subsequent coats. After curing, a light intermediate sanding is recommended to remove small imperfections and ensure an even finish.
Apply subsequent coats with care, scrupulously abiding by the manufacturer-recommended curing times. Avoid applying your varnish in excessively damp weather. The number of coats of varnish to be applied to a wooden surface, particularly in a nautical context, depends on both the type of varnish chosen and the level of protection required. In the case of traditional varnishes, particularly marine varnishes, several coats are essential to guarantee effective, long-lasting protection against weathering.
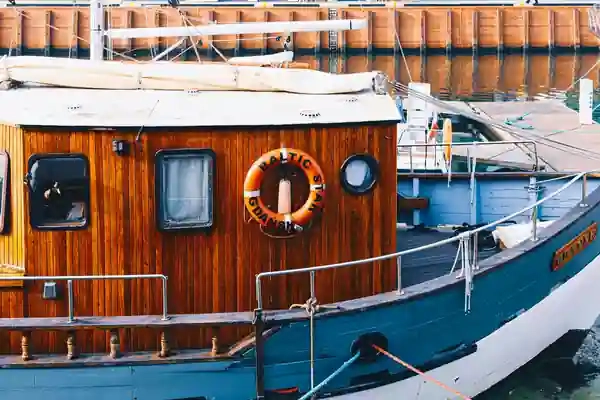
Each successive coat plays a specific role. The first lightly penetrates the wood fibers to ensure proper bonding, while subsequent layers reinforce the protective barrier. The result is a homogeneous, thick and resistant skin. This layer is then able to withstand humidity, salt, friction and, above all, UV rays, which rapidly degrade surfaces exposed to the elements. In general, a minimum of four coats is required for wood to start being properly protected. However, eight to ten coats are required to maximize durability, perfectly smooth the surface and achieve a flawless gloss or satin finish.
Working in successive coats, interspersed with fine sanding, also helps to avoid early cracking or flaking, ensuring greater flexibility and better resistance of the varnish film over time. The final coat must be applied with particular care to ensure a perfect finish and maximum protection against exterior aggression.
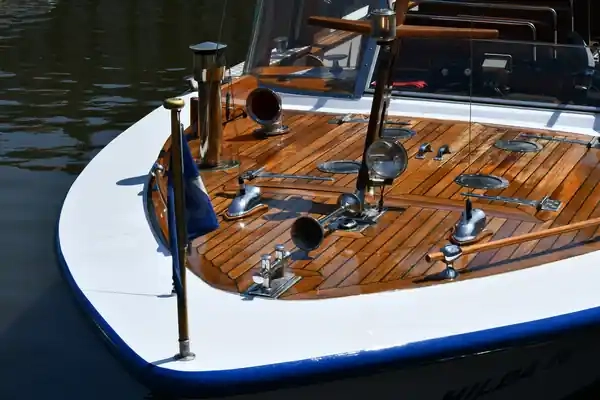
Varnish care
Varnish maintenance is essential to preserve the beauty and strength of the wood. After every trip out to sea, rinse the boat with fresh water to remove any salt residues that could alter the varnish surface. Regular inspection will help identify any areas of deterioration before they become more serious. If the varnish starts to dull or flake, you can apply a maintenance coat to restore its shine and extend its life. In cases where the varnish is too damaged, sanding followed by reapplication is usually necessary to restore effective wood protection.
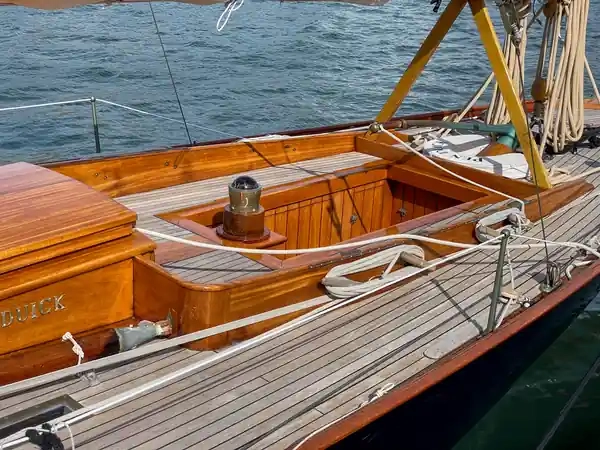
However, it is sometimes possible to carry out localized repairs, without having to rebuild the entire surface. This can be considered if the damaged areas are well-defined and the original varnish is not too worn overall. To carry out a localized touch-up, first carefully sand the affected area, degrading the edges slightly to avoid a visible boundary between old and new varnish. Next, clean the surface to remove any dust or greasy residue. Then apply several thin coats of varnish, respecting the curing times between each coat. Once the varnish has hardened, light sanding or even polishing can be used to blend the touch-up into the rest of the surface. Although this method does not always offer perfect uniformity, it is a practical solution for stretching the lifespan of the coating between complete refits.
Varnish: demanding but effective protection
The choice of varnish depends on a number of criteria, including the environment in which the boat is used, the level of maintenance required and the desired aesthetic effect. For traditional boats requiring frequent maintenance, a classic single-component varnish remains a reliable option. For those seeking maximum protection against ultraviolet rays and salt water, a combination of epoxy resin and polyurethane varnish is often recommended. Finally, for those who prefer a natural finish and simplified maintenance, satin-finish oils or varnishes are an interesting alternative.
By choosing the right varnish and following the correct coating and maintenance procedures, you can considerably extend the life of a wooden boat, while enhancing its natural beauty. However, this requires rigorous maintenance – just like the rest of the boat! That said, it’s all for the best: good varnishing doesn’t just look good, it also guarantees the boat’s resistance and durability in the face of the most aggressive marine elements.
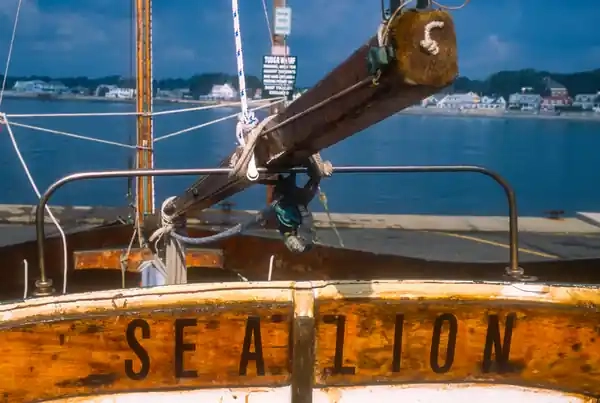